SOCAR Polymer işçi axtarır - VAKANSİYA
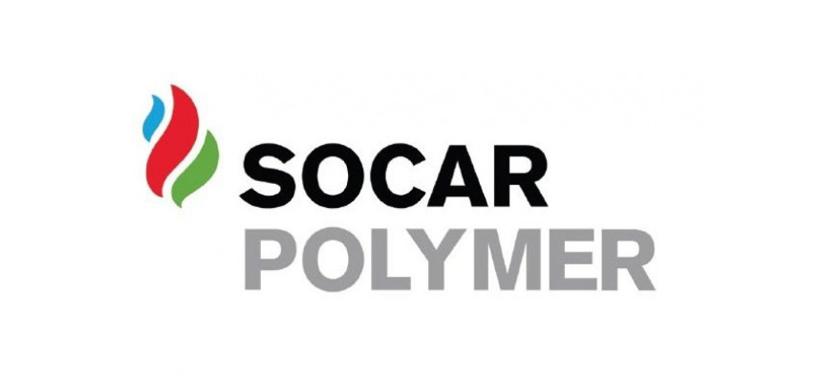
Title: Reliability Engineer
Department: Engineering and Maintenance
Location: Sumgait
JOB SUMMARY
Reliability Engineer with experience on rotating and static equipment with an emphasis on reliability. The Reliability Engineer will be the owner of the reliability engineering function for the plant, ensuring and implementing best practices to maintain consistent and reliable equipment operations.
Requires expanded conceptual and practical knowledge in own job discipline and broadens capabilities, good technical knowledge about equipment performance and failures. Additionally, a good work ethic and strong interpersonal skills are required since the position involves daily contact with customers and end users.
track the production losses and abnormally high maintenance cost assets, then find ways to reduce those losses or high costs. The reliability engineer (in full partnership with the maintenance and operations team) develops a plan to eliminate or reduce the losses through root cause analysis, obtains approval of the plan and facilitates the implementation.
manage risk to the achievement of an organization’s strategic objectives in the areas of environmental health and safety, asset capability, quality and production. Some tools used by a reliability engineer to identify and reduce risk include:
PHA – Preliminary hazards analysis
FMEA – Failure modes and effects analysis
CA – Criticality analysis
SFMEA – Simplified failure modes and effects analysis
MI – Maintainability information
FTA – Fault tree analysis
ETA – Event tree analysis
Reliability Engineer to be involved in the design and installation stages of projects for new assets and modification of existing assets.
The Reliability Engineer is also responsible for partnering to establish a “Continuous Improvement and Zero Loss” culture. The position provides support and coaching within the plant in loss elimination, risk management and life cycle asset management (LCAM).
JOB DUTIES
• Report to the Discipline Engineers Team Lead and work under his overall supervision and directions.
• The reliability engineer is responsible for adhering to the life cycle asset management (LCAM) process throughout the entire life cycle of new assets.
• Guides efforts to ensure reliability and maintainability of equipment, processes, utilities, facilities, controls and safety/security systems.
• Develops engineering solutions to repetitive failures and all other problems that adversely affect plant operations. These problems include capacity, quality, cost or regulatory compliance issues. To fulfil this responsibility, the reliability engineer applies:
• data analysis techniques that can include:
• Statistical process control;
• Reliability modelling and prediction;
• Fault tree analysis;
• Weibull analysis;
• Six Sigma (6σ) methodology;
• Root cause analysis (RCA) and root cause failure analysis (RCFA),
• Failure reporting, analysis and corrective action system (FRACAS).
• Professionally and systematically defines, designs, develops, monitors and refines an asset maintenance plan that includes value-added preventive maintenance tasks.
• Effective utilization of predictive and other non-destructive testing methodologies designed to identify and isolate inherent reliability problems.
• Provides technical support to production, maintenance management and technical personnel.
• Applies value analysis to repair/replace, repair/redesign and make/buy decisions.
• Monitor plant/equipment trends to ensure the best possible operation and reduction of planned/unplanned downtime.
• Propose and monitor key performance indicators in accordance with the Best Maintenance Practices.
• reduce technical stoppages in equipment or areas of common occurrence (priority given to areas of the highest incidence or impact). Ensure the systematic review of all line, processes, and utilities that are critical to the business and those where failure can have an unacceptable impact on safety, personnel safety, food safety, environment, or compliance with the law.
• Encourage close teamwork between all functions.
• Ensure the implementation of all repairs/modifications resulting from Gap assessments, plant audits, and notifications and loss improvement activities.
• Ensure that the equipment history, damage code and root cause analysis are completed correctly and analysed regularly for trends.
• Update/Optimize Reliability Engineering tools and guidelines, to minimize unplanned and Planned Downtime, ensure a common approach, administration, and training.
• Facilitate the evolution/refinement of Maintenance activities to minimize planned and unplanned downtime (PM’s, changeovers, etc.).
• This position also requires working knowledge of TPM-PM, Downtime Recording Systems and SAP-PM, and broad experience in multiple Engineering and Maintenance positions. Willingness to embrace new technologies, analysis techniques, and lead improvements is also required.
• Benchmarks equipment reliability performance against industry metrics.
• Identifies equipment deficiencies using statistical report data measuring site equipment performance.
• Reviews and analyses existing predictive and preventive maintenance tasks and schedules to ensure optimal use of manpower and equipment.
• Lead the site condition monitoring and predictive maintenance program to enhance mechanical integrity.
• Develop processes, policies and procedures for maintenance and plant engineering.
• Rationalize PM schedules based on need and sound engineering practice.
• Leads component failure analysis program.
• Provides technical expertise and coaching to implement prevention methods.
• Root-cause and Root-cause Failure Analysis (RCA, RCFA).
• Creates Equipment Reliability Strategies based upon Top Opportunity List, Critical Equipment List, and identified plant/business needs.
• Validates Electronic Recording and Reporting System (ERS) implementation and closes gaps to improve/sustain reliability improvement.
• Evaluates effectiveness of individual aspects of the PPM program by showing quantitatively the impact of failures and Predictive Preventive Maintenance (PPM).
• Optimizes PPM activities, on an on-going basis, to support overall productivity improvements.
• Develops and maintains, as requested, a model that identifies the unit operations, equipment, process, etc. that identifies the value of opportunities for improvement.
• Uses reliability engineering principles and tools (Weibull, RCI, FMEA) to identify and eliminate negative reliability trends and equipment performance.
• Participates in plant health study and efforts to implement corrective action to maintain or improve plant health.
• Develops and implements the Facility Reliability Strategy.
• Serves as RCI Team Leader with proven RCI skills, coaches others in RCI facilitation and ensures strong RCI/CAPA fundamentals are practiced within the unit.
• Provides front end loading support for plant Turnarounds.
• Provide input and guidance to other engineers, technicians, and plant personnel on critical Reliability Principles, Predictive and Preventive Maintenance Strategies, and Operating Principles of common rotating and fixed equipment.
• Identify, Plan, and Execute component-level Reliability Improvement Projects as necessary to incrementally improve plant performance.
• Support the plant-wide lubrication program and work to continuously improve the program by implementing industry best practices.
• Review engineering specifications/drawings and propose design modifications to improve reliability within cost and other performance requirements.
• Oversee/interact with maintenance regarding maintenance repairs, repair plans, equipment installation, quality assurance requirements, etc.
• SAP PM Key user- responsible for work management business process and new enhancements, custodian of the existing CMMS functionality, to ensure that all functions and processes are working in a good manner.
• Ensuring compliance with health and safety legislation.
• SPA for maintaining MTBF equipment.
• Accountable to track and develop way forward to investigate and rectify failure of equipment.
• Monitor and track top 10 bad actors of major equipment.
REQUIREMENTS
Functional
• Recognized skills in Engineering and Maintenance.
• Knowledge, understanding, and passion for continuous improvement methodologies.
• Knowledge and understanding of the cost drivers of Maintenance in manufacturing operations.
• Good working knowledge of CMMS systems (SAP preferred) with the ability to mine and analyze data for trends/reports.
• Knowledge of the different crafts skills, duties, and capabilities.
• Knowledge of Process Safety Management (PSM).
• Knowledge of mechanical and electrical systems, preventive and predictive maintenance technologies, and condition monitoring and fixed time maintenance strategies.
• Familiarity with Non-Destructive Testing methods.
• Working within a Computerized Maintenance Management System (CMMS).
• Willingness to be available and on call 24/7 as needed due to business conditions.
• Other preferred skills.
• Familiarity with international standards such as API510&570&653, ASMEB31.1&B31.3, NBIC, NACESP0294.
• Working with Highly Hazardous Chemicals/High Hazard Process.
• Manufacturing experience which includes exposure to Safety, Health, Environment, Quality, Maintenance and Continuous Improvement systems and tools.
• Root Cause Failure Analysis and Incident investigations
• Relevant technical knowledge (mechanical; instrument; electrical equipment).
• Understanding safety precautions involved while working high powerful electrical equipment.
• Solid understanding of control and monitoring devices.
• Strong computer skills (Microsoft Office, Outlook).
• Strong knowledge of maintenance programs and their integration into SAP PM.
• Ability to work independently, but also as part of a team when interfacing with various disciplines (i.e. Instrumentation and control, process, mechanical and reliability etc.).
• Familiar with International and Local standards, best practices and value practices.
Behavioral
• Teaching and training ability.
• Gives and receives feedback.
• Communicates technical issues well.
• Process and Technical Leadership.
• Interpersonal Effectiveness.
• Excellent verbal and written communication skills.
• The capacity to understand a range of engineering functions and procedures.
• Teamworking skills to work cooperatively and liaise with people at all levels.
• Good diagnostic and problem-solving skills.
• The confidence to respond positively when under pressure.
• People-management skills.
• Able to organize, coordinate, and direct users and teams.
• Excellent presentation skills.
• Project Engineering/Management.
• The ability to interact professionally with a diverse group, including managers, technicians, operators and subject matter experts.
• Demonstrated collaborative problem solving, excellent planning and organizational skills.
• Strong analytical skills.
• Utilization of data in a timely manner.
Education and experience
• Minimum 5 years of hands-on verifiable experience in rotating and static equipment at manufacturing facility (chemical industry preferred), Engineering and/or Maintenance, Reliability and Manufacturing field with direct experience in leading and engaging technicians with equipment modifications and improvements in a production and/or manufacturing environment. TPM experience, Maintenance Planning and/or supervision a plus.
• English and Azerbaijani professional working proficiency.
• It is desirable that he/she would also be able to speak and write in Russian.
• SAP Maintenance module experience is required
• Classical understanding of core maintenance principles required
o Predictive Maintenance
o Preventative Maintenance
o Precision Maintenance
o Maintenance workflow process theory
o Business Criticality
o Planning and Scheduling
o Mechanical Integrity
o Lifecycle costing
o Quality Assurance methods
• Chemical or petrochemical industry experience required.
• Solid understanding of industrial equipment and their parts
• Strong knowledge of maintenance programs and their integration into SAP PM;
• Good knowledge about practical application of Corrective, Predictive and Preventive maintenance strategies
• Knowledge and experience about the usage of tools and techniques used in repair, inspection and overhaul;
• Bachelor’s and/or master’s degree in engineering (Industrial, Mechanical, Electrical, Process, Chemical or equivalent) strongly preferred or equivalent work experience and relevant certifications (i.e., SMRP, CMRP and ICML certification desired or willingness to complete in 12 months).
APPLICATION PROCEDURE
Interested candidates should follow the link below:
https://socarpolymer.az/en/career/experienced-professionals/
The above vacancy is addressed to nationals of Azerbaijan or with permanent residency in Azerbaijan. All eligible applications for the advertised post will be assessed and given equal opportunities.
Application closing date: June 02, 2020